Cross Wedge Rolling - Machines
Cross-Wedge Rolling Machines are used for forming axisymmetric parts by altering their cross section. Three baseline types of cross-wedge rolling machines are available that use different rolling methods: cold, warm and hot cross-wedge rolling. To meet our customers' individual demands, we produce specialized equipment. Due to the special modular design of all models of rolling machines, their functional capabilities and automation level can be widened step by step. Special purpose machines may also be produced using separate parts. All models of cross-wedge rolling machines can be equipped with an automatic die change device, which allows to reduce the die change time to 5-10 minutes. |
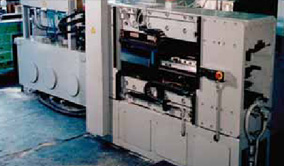 |
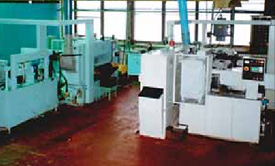 |
|
Model |
WRL2510 |
WRL3512 |
WRL6009 |
WRL6321 |
WRL8012 |
Perform diameter, mm |
15-25 |
20-40 |
30-60 |
30-65 |
40-80 |
Perform max. length, mm |
350 |
350 |
350 |
350 |
320 |
Single-piece rolling output (depending on RF current heating power), parts/hour* |
500-720 |
450-600 |
300-400 |
360-450 |
240-300 |
* The output of pair rolling is doubled. |
WRL machines are designed to produce parts like solids of revolution by the method of cold, warm (t=500-700°C) and hot (t=1000-1250°C) rolling. Warm rolling is used for production of finished parts or preforms with minimum stock for further machining (grinding). The dimensional accuracy and surface quality are insignificantly lower than in cold rolling. Hot rolling is applied to form complexly-shaped parts with a 4-5 draft ratio for one travel. Dimensional accuracy and surface quality are determined by wider tolerances, compared to cold or warm rolling, and as a rule, require further machining. WRL machines have one (upper) moving die. A slider is installed on rolling-contact bearings with automatic clearance adjustment allowing to minimize friction losses and avoid clearance in guides when the slide is heated during the rolling process. All the machine components which are in contact with a hot billet have intense water cooling, allowing to minimize the time required for the thermodynamic process stabilization. A pyrometer adapted to any presence of scale on the billet provides for high-accuracy control of the billet temperature and to produce high-precision parts.
WRL TN Series
WRL TN machines is a further development of WRL Series designed to produce parts like solids of revolution by the method of warm and hot rolling. WRL TN machines have two movable dies that allows to use wedge die up to 3.5m in length, and produce preforms up to 200 mm in diameter.
|
Model |
WR L2507 TN |
WRL 6316 TN |
WRL 8020 TN |
WRL 10025 TN |
WRL 1 3030TN |
WRL 16030TN |
WRL 20035TN |
Perform diameter, mm |
7-25 |
30-65 |
40-80 |
60-110 |
70-130 |
80-160 |
100-200 |
Perform max. length, mm |
250 |
350 |
500 |
600 |
600 |
800 |
1200 |
Single-piece rolling output (depending on RF current heating power), parts/hour* |
720-900 |
450-600 |
360-450 |
120-240 |
90-180 |
70-150 |
49-90 |
* The output of pair rolling is doubled. |
|